How Skateboard Decks Are Made
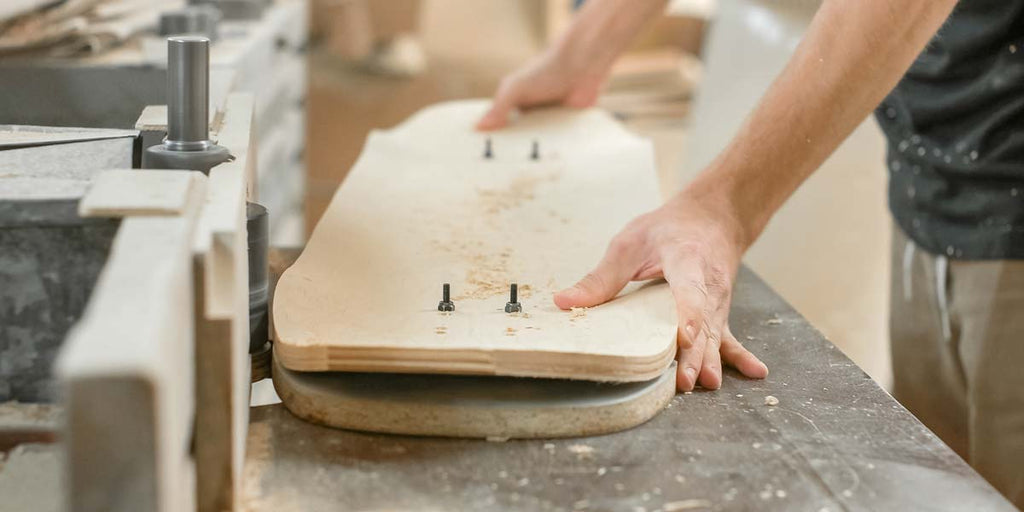
Whether you’re an old school skater or a rookie learning the ropes, learning the manufacturing process of skateboard decks can be a huge benefit to your performance. How? Understanding how your board is put together — and what the differences are between types of manufacturing processes — can help you choose one that’s better quality and will last you longer. Here’s your basic breakdown of how skateboard decks are made.
Wood Treatment
Skateboard decks are almost always constructed of a maple wood that comes from the Great Lakes area of the U.S. and Canada. The maple trees in this particular region have short growing seasons and tall trees with a very high density (and in turn, high durability).
Once the logs from this area are sent to the mill, they can be stored for up to 3 months before being treated. Before being cut into veneers, they’re soaked in water for hours to soften them enough to be sliced properly. Once they reach about 50% moisture, the logs are spun at a high speed against a blade, creating thin veneers that are dried before being sent to the manufacturer.
Veneer Coating
The manufacturer then takes each veneer and is fed into a glue machine by hand. The veneer, usually about one-twentieth of an inch, is evenly coated with a water-based glue on both sides.
Layering and Molding
The stacking of the veneers and the molding process are one of the most important processes in deck manufacturing. After being coated, 7 veneers are stacked in a specific order inside of a mold. This mold determines the concave of the board, as well as the nose and the tail. In alternating layers, the veneers are placed according to the grain direction, with some of them going lengthwise and some going perpendicular. This helps to strengthen the board.
The length of time that the veneers sit in the mold varies depending on the manufacturer. Generally, the longer they sit in the mold, the more naturally they’re able to set, which provides greater durability in the long run. Some manufacturers use heat to speed up this process, and although it doesn’t destroy the boards completely, it can weaken the natural fibers of the maple wood.
Drilling and Shaping
After the veneers set, the deck is removed from the press and eight holes are drilled for mounting the trucks. Each deck is then hand-shaped with a band saw using a premade template, sanded and coated with a sealant before being sent for screen-printing.
Design
The design process is a lengthy one that usually takes place not at the manufacturer, but within the company that is purchasing from the manufacturer. However, once graphics are decided on, they are painted onto the deck via a custom screen-printing machine, before being packaged and shipped to the company.
Knowing how your deck is constructed can help you recognize a quality one when you’re shopping, as well as understand how to best care for it so you can extend its lifespan and get the most out of your board.
- Outdoors Staff
Comments 0